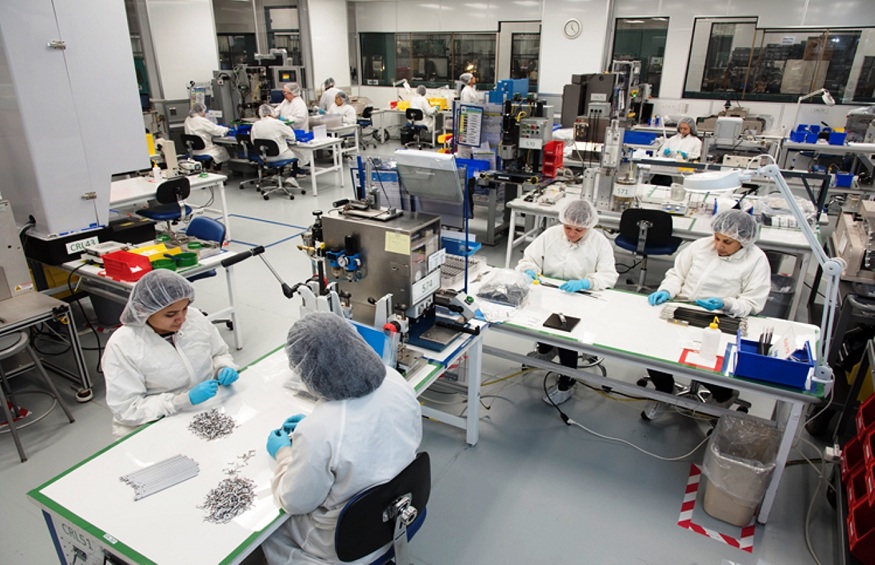
Design Control Requirements – A Brief Description
The medical industry is considered more sensitive as varying levels of risks are involved in the manufacturing process of the devices that must be carefully managed. The Food and Drug Administration requires proof that the medical device produced assures patient safety. The first step for manufacturers of medical devices in meeting the FDA’s requirements is to set up a robust design and development process and develop medical devices under design controls. The design control requirements delineated within 21 CFR Part 820 – Section 820.30 helps in building a quality medical device that is safe and effective when it comes to users’ health.
There are three classes of medical devices recognized by the FDA – I, II, and III – depending on a product’s intended use, indications for use, and the level of risk associated with the product. FDA-mandated design controls describe a formalized approach in developing class III or class II devices, and certain class I devices. There are many layers of documentation that must be submitted to the FDA to demonstrate how you have ensured the safety and efficacy of your new product.
To find out which class your product belongs to, you can visit the FDA’s Medical Device Classification database and search for a part of the device name, or, Device Classification Panel, if you know the medical specialty related to your device. Moreover, you may seek the assistance of a regulatory consultant who can help your team understand the FDA regulations that pertain to your specific circumstances.
Design Control Requirements
Having determined the need for medical design controls requirements, you now need to structure your development process around these requirements. Below are the core components of your product design process that are required for design controls.
User Needs: The procedure requires the manufacturer to clearly define the design control procedures of the device that fulfills the specified design requirements.
Design & Development Planning: The procedure requires the manufacturer to establish and maintain a design and development plan that identifies and describes the specifics of dealing with each of the design controls in the design and development process.
Design Inputs: The procedure requires the manufacturer to describe the exact specifications of the product that ensure the appropriateness of the device design requirements, what the device will do, and how it will meet the needs of the user and patient.
Design Outputs: The procedure requires the manufacturer to document the exact design, materials, and components needed in building the product, and could include drawings and diagrams.
Design Review: The procedure requires the manufacturer to plan and conduct formal documented reviews at appropriate stages of the product development that ensure that the product is on track.
Design Verification: The procedure requires the manufacturer to verify the product design to ensure its conformity with design input requirements.
Design Validation: The procedure requires the manufacturer to validate the devise design to ensure that devices conform to users’ needs and intended uses.
Design Transfer: The procedure requires the manufacturer to ensure that the production of the medical device is correct and in conformity with the design.
Design Changes: The procedure requires the manufacturer to ensure design controls apply to the entire lifespan of a medical device.
Design History File: The procedure requires the manufacturer to maintain a design history file for each type of device to ensure that the approved design plan and the requirements are fully met.
It goes without saying that design control requirements are an important aspect of your product development process. In spite of being challenging, design controls not only guarantee FDA approval but also ensure a better, safer medical device.